Refrigerated ISO Container vs Our Cold Storage Containers
MEET THE WORKHORSE : Great, but not Great for Everything
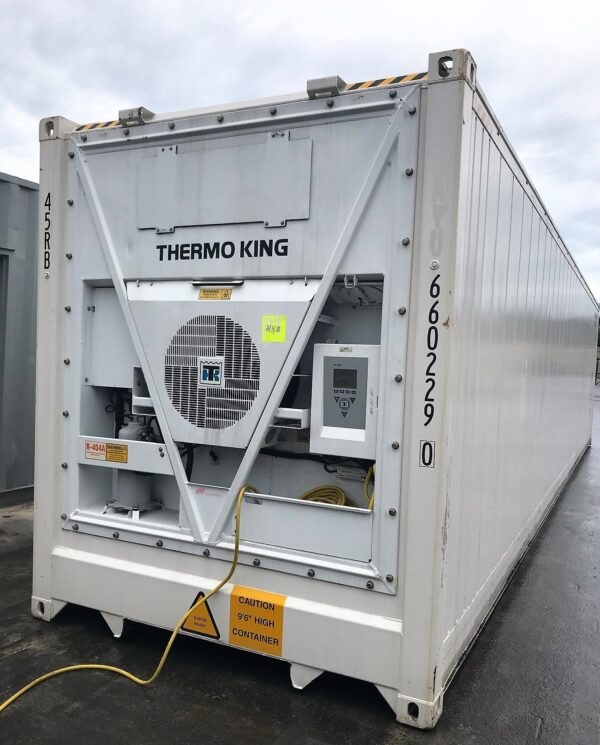
There is no greater work horse of the INTERNATIONAL cold storage industry than the ISO Refrigerated Container
Starting being used in international shipping in 1968. This innovation allowed for the transportation of temperature-sensitive goods over long distances, revolutionizing global trade in perishable products.
They have downsides when used in NON-SHIPPING Applications
- Heavy and Hard to Maintain: The weight of the cooling unit on an ISO refrigerated container ranges from approximately 500 to 1,000 kilograms (about 1,100 to 2,200 pounds). This means maintenance by HVAC Repairmen is nearly impossible outside of a port.
- Difficult to adapt to non-international cargo uses. They run Three phase power and most businesses in US run on Single Phase Power.
- Cold storage units can be approximately 20-30% more energy-efficient than ISO refrigerated containers. The doors on a Reefer Container prioritizes access over the efficient holding of items at temperature.
3 Phase Power Is Great But 99.9% of Business Sites Can't support It
The cost of converting an ISO refrigerated container’s electrical system from three-phase to single-phase can vary widely based on several factors, including the size and power requirements of the refrigeration unit, the type of conversion equipment used, and labor costs. Here’s a rough breakdown of potential costs:
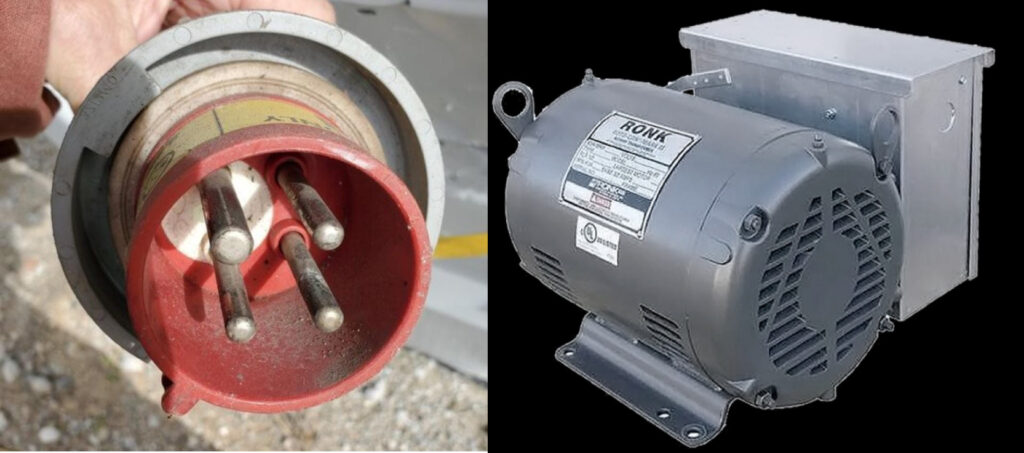
Phase Converter:
Rotary Phase Converter:
Cost: $2,000 to $5,000, depending on the size and capacity.
Installation: Additional $500 to $1,500 for installation and setup by a qualified electrician.
Static Phase Converter:
Cost: $200 to $800, suitable for lower power applications.
Installation: Additional $200 to $500 for installation.
Variable Frequency Drive (VFD):
Cost: $1,500 to $5,000, depending on the size and features (including single-phase to three-phase conversion capability).
Installation: Additional $500 to $1,500 for setup, which may include programming and configuring the VFD for the specific motor and application.
Transformers and Wiring:
If voltage adjustment is necessary, a transformer might be required to step up or step down the voltage, adding $500 to $3,000 to the cost, depending on the capacity.
Additional wiring and electrical components may cost $300 to $1,000.
Labor Costs:
Labor costs can vary significantly depending on the region and the complexity of the installation. A qualified electrician may charge $75 to $150 per hour, and the job may take anywhere from a few hours to a full day.
Estimated Total Cost:
Low Estimate: Around $2,500 to $3,500 (using a static phase converter or a low-end VFD, minimal additional equipment, and lower labor costs).
High Estimate: Up to $10,000 or more (using a high-capacity rotary phase converter or advanced VFD, additional equipment like transformers, and higher labor costs).
These estimates are general and can vary significantly based on the specific circumstances of your setup, local market prices, and the specific requirements of the refrigerated container and its refrigeration unit. It’s advisable to consult with a qualified electrician or engineer to get a more accurate estimate tailored to your needs and ensure the conversion is done safely and in compliance with electrical codes.
Why Wilm Cold Storage Containers are the Smarter Choice Over ISO Refrigerated Containers
While ISO refrigerated containers are essential for international shipping, they are often less suitable for on-site, non-shipping applications. Their size and heavy-duty cooling units make them difficult to maintain outside ports, and they require complex power conversions incompatible with standard business setups. By contrast, Wilm Cold Storage containers are designed for efficient, low-maintenance cold storage on business sites without the need for costly modifications.
- Ease of Maintenance: Wilm Cold Storage containers have simpler, single-phase 220V power systems suited for on-site use, unlike ISO containers that require expensive phase converters and special wiring.
- Energy Efficiency: Built with features like heated doors and auto shut-off, Wilm Cold Storage containers are up to 30% more energy-efficient, saving on long-term operational costs.
- Adapted for Business: Lightweight and flexible, these units provide accessible cold storage without the need for costly, labor-intensive maintenance associated with heavy ISO container cooling units.
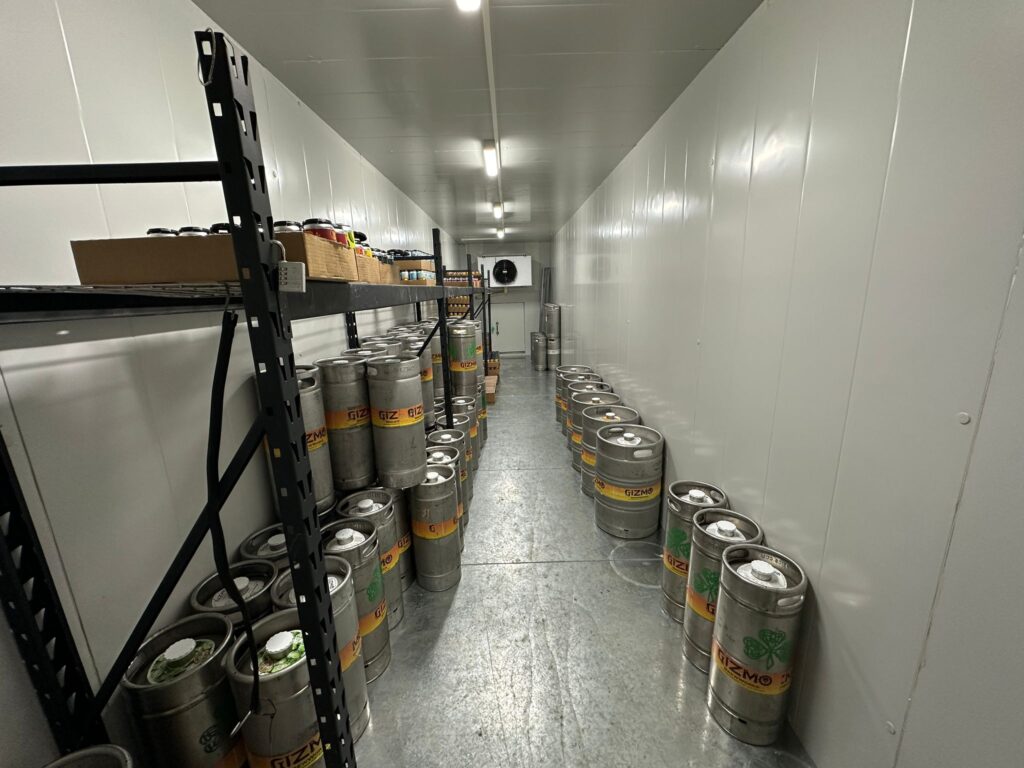